If you're running an operation that involves machining that is small CNC located in your garage, or an important manufacturing enterprise, you've likely bought a few final mill sets to meet your requirements.
You are probably aware that drill bits can only be used in the direction of axial however, cnc end mill provide broader capabilities by allowing you to profile, trace and face. This means you need to make frequent changes to your tool when you work with pieces that require plunging, countersinking profiling, grooving or chamfering. What would you do if we said there were ways to cut down on downtime and keep your machine in good working order?
The same is true in the case of cutting tools. Machining terminology isn't exactly the same to a layman. {In the world outside it is clear that the letters end mills for sale are frequently used interchangeably, but that can cause confusion when referring to the particular tooling used in CNC machines. CNC machines for industrial use (Computer Numeric Control) machines use rotating cutting tools known as end mills to remove material.
End mills are designed specifically for milling, but they can also be utilized in other applications. End mills are able to be utilized for roughing and slotting, as well as for finishing. End mill sets often include center-cutting heads, which permit plunging cuts as well as countersinks that are chamfered to support flush screws.
The right pcd end mill cutter requires you to determine the nature of the work you'll work on. This will help you narrow your tool selection so you only purchase mills which will actually be used in the near future. Let's go over the most commonly used considerations.
Materials
It is essential to understand what materials you will be working with prior to deciding on the tools. For instance, plastic performs quite differently from steel, which is why they require different methods of machining. Before purchasing tools, it is important to think about the geometry sharpness, shape, as well as the mechanical properties of your tool. This will help increase the efficiency and precision while also saving time and money by prolonging the lifespan of your tools.
Flute count
The flute count determines how many contact points your tool has with the material as well as the efficiency of its chip evacuation. For soft materials, a low flute count is preferred as it will provide a higher chip clearance rate and heat control. However, finishing operations usually benefit from a higher flute count. A mill that has 5-14 flutes will produce superior results as well as a more polished surface.
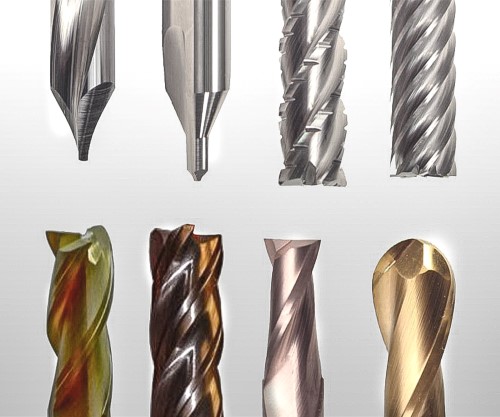
Coating
High-temperature refractory tools are required to machine ferrous alloys, hardened steels and woods. Carbide end mill sets are able to withstand extreme temperatures and rotation speeds without losing sharpness or the structural stiffness. This isn't only beneficial when you are working through lots of materials as it keeps heat under control without sacrificing precision. Hardwoods can also be machined with an carbide coating as it makes it easier to work with the material.
Summary:
It is essential to take into account the specific needs of the work and the materials you will be working with when selecting tools. Additionally, make sure to choose a tool set with high-temperature refractory properties when you intend to work with hard materials. Be aware of the effects of coating choices on your process.
Comments
Post a Comment